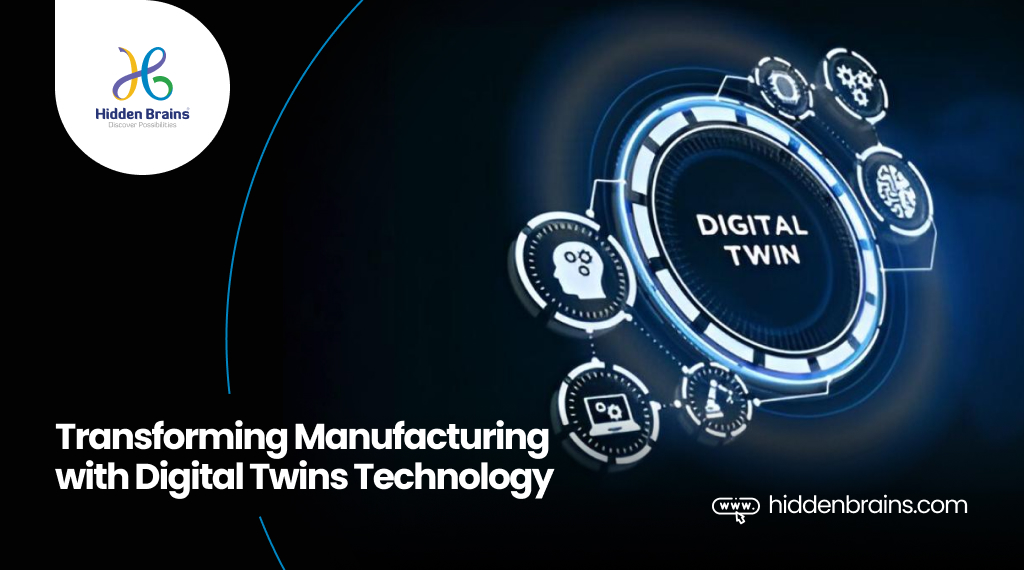
Digital engineering has witnessed various challenges in recent years, such as disconnected historical product data, lack of boundary conditions, and dynamic global scenarios. Challenges like growing competition and complex design structures can also make the design engineering process complicated and tiresome. However, the rapid advancement in Artificial Intelligence and analytics has helped industries embrace digital twin manufacturing, a game-changer in improving product design and development.
Design engineering has shifted from traditional knowledge-based models to a data-driven framework, allowing a cohesive relationship between design and modeling methodologies, operational data, and simulation solutions. The application of digital twin technology is growing phenomenally and changing how businesses manage their product development workflow.
Digital twin technology brings the physical and digital environments closer, enabling businesses to transform how products are designed, built, and marketed. This blog post looks at what digital twin manufacturing is, why it is advantageous, and how it can revolutionize the future. So, stay tuned till the end.
Table of Contents
What Is Digital Twin in Manufacturing?
Simply put, digital twin technology is essential to innovative product development. This technology allows businesses to build a virtual replica of a tangible product or a manufacturing process. It can also replicate a new system or solution that has yet to be developed. In recent years, heavy industries have leveraged digital twin manufacturing using real-time data and advanced simulation tools.
From $12.91 billion in 2023, the digital twin industry is expected to reach $259.32 billion by 2032, indicating its growing demand among the manufacturing enterprises.
Digital twin technology can also replicate or imitate the performance, features, and functionalities of a physical object with ease. The crux of digital twins is engineering an environment that recreates an entity of the real world in a live and evolving model. This is made possible by data flow from the physical product to engineers through sensors and IoT (Internet of Things). While the physical object performs its function, the digital twin acquires data feedback and real-time analysis or predictive or optimal control.
Also read: How AI is Transforming the Energy Sector?
Benefits of Using Digital Twins in Manufacturing
Digital twins manufacturing helps engineering firms and various industries to compare products and evaluate their performance under predetermined manufacturing conditions. With the help of this technology, manufacturers can use a vast amount of production data to streamline their manufacturing process.
Digital twins manufacturing offers a wide range of benefits. By leveraging virtual replicas of physical assets, businesses can unlock unparalleled efficiency, innovation, and sustainability in their operations. Let’s check them out.
1. Improved Product Design and Innovation
Digital twins help manufacturers design and test product prototypes in virtual space before making real ones. The digital model lets us quickly build prototypes and test products virtually, reducing development time and minimizing production mistakes.
Also Read: 15+ Top Software Development Trends to Look for in 2024
2. Enhanced Production Efficiency
Businesses can improve their production efficiency when digital twins process current data streams. Manufacturers use digital twins to find production problems and optimize processes to produce more and waste less time due to equipment halts.
3. Reduced Cost, Waste, and Energy Consumptions
Digital twin technology lets manufacturers test without actual prototypes and makes production smarter to reduce materials waste costs. This approach identifies efficient manufacturing processes that help save energy and minimize material waste.
4. Real-Time Monitoring and Predictive Maintenance
Industries use Digital twins manufacturing to analyze current data and detect maintenance needs before problems appear. Analysis of real-time data from digital twins enables manufacturers to schedule maintenance well before failures happen, which results in immediate improvements in production efficiency and equipment durability.
5. New Revenue Streams
Digital twins help businesses discover new opportunities for revenue by offering predictive analytics and customized upgrade solutions. By replicating new products virtually, manufacturers can quickly scale up whenever they want to.
6. Personalized Products and Improved Quality
Companies can produce customized solutions based on each customer’s needs through Digital twins manufacturing. This capability creates better customer experiences through tailored, high-quality product solutions.
7. Improved Quality and Customer Satisfaction
Digital twins let us test products extensively while finding ways to enhance their performance. Manufacturers use tracked customer usage data to identify gaps and faults, improve their products, and maintain customer satisfaction.
8. Traceability from Start to Finish
With digital twins, businesses can easily trace each product’s lifecycle from conception to delivery. This transparency enhances accountability, ensures regulatory compliance, and supports effective lifecycle management.
Key Components of Digital Twin Manufacturing
Digital twin technology is built on several key components. These components interact with each other and function simultaneously to create a near-perfect virtual model of a physical product. Let’s check out the key elements of it.
1. Physical Asset
The real-world product, system, or process that the digital twin represents.
2. Digital Replica
A virtual model that mirrors the physical asset in design, behavior, and performance.
3. Data Sensors and IoT Devices
Sensors embedded in the physical asset to collect real-time data on operations, performance, and environmental factors.
4. Data Integration and Connectivity
Systems to ensure seamless communication between the physical and digital twins, enabling real-time data exchange.
5. Simulation and Analytics Tools
Advanced software and algorithms to simulate scenarios, predict outcomes, and analyze performance.
6. AI and Machine Learning
Intelligent systems to provide predictive analytics, automate decision-making, and continuously optimize operations.
7. Cloud Computing and Storage
Scalable platforms to store and process the massive data generated by digital twins.
8. User Interface
Intuitive dashboards and visualization tools for monitoring, analysis, and decision-making.
Also read: Explore Custom Software Product Development with AI
Top Use Cases of How Digital Twins are Used in Manufacturing
Digital twins have revolutionized smart product development, offering a versatile and efficient approach across various product lifecycle stages. By enabling real-time insights, accurate simulations, and seamless collaboration, digital twin technology is transforming how businesses innovate and deliver solutions.
From factory floor optimization to decreasing downtime, here are the top four applications of Digital twins manufacturing.
1. Conceptualization and Prototyping
Digital twins simplify the initial stages of product development by enabling virtual conceptualization and prototyping. Designers and engineers can create accurate digital models, experiment with various designs, and test feasibility—all without the cost and time associated with physical prototypes. This immersive approach allows stakeholders to visualize and refine concepts early, ensuring alignment with project goals.
2. Simulation and Testing
Engineers can use digital twins to assess product performance through virtual experiments without fundamental components. Engineers evaluate digital product replicas when exposed to difficult circumstances to study their functioning and anticipate problems. Employees can learn new operations through virtual training since this method protects their safety and tools.
3. Optimization of Manufacturing Processes
Industries use Digital twins manufacturing to optimize their manufacturing workflow. It helps them streamline the process by providing real-time insights and predictive analytics. With the help of digital twin manufacturing, production managers can track production lines, identify inefficiencies, and deploy solutions from anywhere. In addition, digital twins engineering offers accurate space planning and plant floor optimization, allowing manufacturers to set up layouts and equipment with minimum space and maximum productivity.
4. Life-cycle Management and Post-market Support
Digital twins extend their utility beyond production, playing a crucial role in lifecycle management. By tracking the performance and health of products, businesses can intuitively locate maintenance and repair documentation, schedule predictive maintenance, and ensure long-term reliability. Virtual site visits and inspections eliminate the need for travel, streamlining global operations.
Real-life Examples of Digital Twin Manufacturing
Digital twins engineering enables companies to optimize their manufacturing processes and product qualities while staying competitive in terms of pricing and features. The following table will showcase 10 inspiring examples of leading global manufacturing brands that have implemented this technology.
Manufacturer | Use Cases | Benefits |
Siemens | Predictive maintenance for industrial equipment, optimizing production processes, virtual commissioning of new plants | Reduced downtime, increased efficiency, improved product quality |
General Electric | Monitoring and optimizing performance of jet engines, power plants, and other industrial equipment | Enhanced asset performance, reduced maintenance costs, improved fuel efficiency |
Boeing | Designing, testing, and manufacturing aircraft, simulating flight conditions | Improved aircraft design, reduced development time, enhanced safety |
Rolls-Royce | Predictive maintenance for aircraft engines, optimizing engine performance | Reduced maintenance costs, improved engine reliability, increased aircraft availability |
John Deere | Precision agriculture, optimizing farm equipment performance | Increased crop yields, reduced fuel consumption, improved soil health |
BMW | Designing and testing new vehicles, optimizing production processes | Improved vehicle design, reduced development time, increased production efficiency |
Johnson & Johnson | Optimizing pharmaceutical manufacturing processes, improving drug delivery systems | Increased production efficiency, improved product quality, reduced development costs |
Procter & Gamble | Optimizing supply chain, improving product design | Reduced supply chain disruptions, improved product innovation, increased customer satisfaction |
PepsiCo | Optimizing food and beverage production, improving supply chain | Reduced production costs, improved product quality, reduced waste |
L’Oréal | Personalized beauty products, optimizing production processes | Improved customer experience, increased product innovation, reduced development costs |
Why Do Manufacturers Need Custom Digital Twin Software?
Companies use custom digital twin software to create exact digital copies of their real-world assets, production methods, and operational frameworks. Custom software adapts perfectly to each business’s needs and helps create precise copies of operations. Manufacturers gain instant operational data through customized digital twins while solving their unique production problems and boosting productivity.
Custom digital twin tools allow businesses to preview their operations and spot upcoming problems without affecting their current running processes. Companies can optimize their strategies in secure virtual spaces without risk, which speeds up their innovation efforts and lowers operational costs.
Custom solutions work well with current systems to build a single system that collects data and helps users make better decisions. Companies that seek market success in the current rapid market growth must use custom digital twin software to boost their operational efficiency, environmental performance, and future business growth.
Complementary Technologies Associated with Digital Twin Manufacturing
Digital twin technology thrives on collaboration with advanced technologies, enhancing its effectiveness and broadening its applications in manufacturing
1. Internet of Things (IoT)
IoT devices and sensors deliver vital real-time information to digital twins that track physical assets. The ongoing data feed enables exact process simulations while monitoring production in real-time and providing accurate manufacturing data.
2. Artificial Intelligence (AI) and Machine Learning (ML)
Digital twin data streams feed AI and ML systems, creating forecasts to trigger automatic processes. These technologies help streamline processes and find problems while forecasting repairs.
3. Virtual Reality (VR)
VR makes digital twins come alive through full sensory engagement experiences. Interacting with virtual replica engineers and operators gives them more profound insights into complex systems, leading to better decisions.
Steps for Developing a Digital Twin for Your Manufacturing Facility
Implementing a digital twin for your manufacturing facility is a complex and strategic process requiring an experienced custom software development partner specializing in cutting-edge technologies.
By following a structured approach, businesses can harness the power of real-time data, predictive analytics, and advanced technologies to optimize production, reduce costs, and drive innovation. Here’s a concise guide to building a practical digital twin for your operations.
1. Define Objectives
Mark down the primary purposes of your digital twin, which are to enhance production efficiency and extend asset life while producing superior products.
2. Collect Data
Use IoT sensors and monitoring devices to collect current data from your buildings, equipment, and business processes.
3. Develop the Digital Model
Build a digital copy with simulation software that matches your real-world environment. Integrate Technologies: Let AI and ML guide our technology as it processes data through the cloud for better predictions and easy connections.
4. Implement and Test
Check if the digital twin works correctly by testing it against actual situations and adjusting it when necessary.
5. Monitor and Optimize
Review the collected data at all times and then improve your model and system operations by processing current information.
How Hidden Brains Empowers Manufacturers with Digital Twin Technology
As your proven software development provider, Hidden Brains brings 21 years of experience to deliver custom applications that serve multiple industries. We created our Production Management Software to improve manufacturing by managing production plans and workflows while ensuring accurate stock tracking. The result? Our solutions boost operational output and quality while simplifying workplace operations.
Our software development services have a strong background in AI, ML, and IoT systems to build advanced digital twin manufacturing technology. We provide advanced features for manufacturers to track operations and predict market trends while optimizing their production processes to lead the competitive market—team up with our experts to modernize your production methods and reach top performance.
Final Words
Digital twin in manufacturing redefines how businesses approach product development, bridging the gap between the physical and digital worlds to unlock unparalleled efficiency and innovation. Manufacturers can optimize processes, reduce costs, and deliver high-quality products that meet evolving market demands by harnessing the power of real-time data, predictive insights, and cutting-edge technologies like IoT, AI, and VR.
As the manufacturing landscape continues to evolve, embracing digital twin technology is not just a choice—it’s a necessity for staying competitive and future-ready. Now is the time to embark on this transformative journey and position your business at the forefront of innovative product development.
Frequently Asked Questions (FAQs)
If you have additional questions regarding digital twins manufacturing and want to hire dedicated developers from us, Check out our comprehensive FAQ section to get all the answers.
1. What is a digital twin in manufacturing?
Manufacturing digital twins creates digital copies of all elements within production facilities, including equipment and production methods. This technology lets users watch operations unfold in real-time and optimize production by turning digital copies of factory systems into live digital displays.
2. How does digital twin technology benefit manufacturers?
Digital twin systems enable manufacturers to design their products better while making their operations more effective, saving money, and maintaining product quality. This system helps companies predict when equipment will need maintenance plus cuts product waste while making custom goods and keeping customers happy.
3. What industries can benefit from digital twin manufacturing?
Industries such as automotive, aerospace, electronics, healthcare, and consumer goods manufacturing can benefit significantly from digital twin technology. Any sector with complex production processes needing enhanced monitoring and optimization can leverage this innovation.
4. What technologies work with digital twins?
Digital twins work seamlessly with technologies like IoT for real-time data collection, AI and ML for predictive analytics, and VR for immersive simulations and interactions. These complementary technologies enhance the effectiveness of digital twins in manufacturing.
5. Why is custom digital twin software necessary?
Custom digital twin software allows manufacturers to tailor the solution to their specific needs, ensuring precise replication of assets, processes, and workflows. This flexibility enhances performance monitoring, decision-making, and overall operational efficiency.
6. What is the future of digital twin manufacturing?
The future of digital twin manufacturing is promising, with advancements in AI, IoT, and edge computing driving its adoption. It is expected to become a standard tool for manufacturers, enabling more innovative, efficient, and sustainable production processes across industries.